Multi-port valve blocks stainless steel
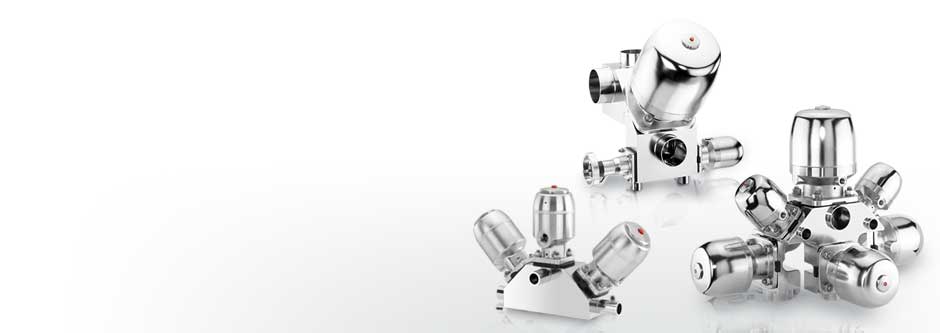
Conventional welded assemblies
Complex processes using welded assemblies are often still being implemented today, more than 20 years after the market launch of the first M-blocks. The valves, fittings and pipe components used for this require a lot of space, a greater installation and welding effort on site and lead to a correspondingly high validation expense. Not to mention a high hold-up volume and larger deadlegs in compliance with the conventional 6D or 3D rules.
GEMÜ solution for safe operation and high-quality products
Over the years, GEMÜ has implemented over 400 different designs and thousands of customized variants of multi-port valve blocks to make processes safer, increase system availability and reduce the life cycle costs of a system as part of a total cost of ownership (TCO) concept.
Consultation, engineering, manufacturing expertise
We begin supporting our customers as early as the planning phase by providing them with ideas and initial drafts. We then implement the design in the 3D CAD system and adjust it to closely meet the requirements of the particular customer. This jointly developed solution is then processed in our highly efficient machine shop. Several thousand blocks, with weights ranging from 0.1 kg to 500 kg, are processed each year on our multi-axis machining centres.
Product advantages
Produced from a single block of material -> no internal welds, fewer fittings and fewer welds thanks to several valve seats in one unit
individually customized design
Integration of valves, measurement and control systems in a single unit; suitable for modular system designs
Certificate of compliance with the order, test certificate, inspection certificate 3.1, inspection certificate 3.2 available on request
Draining and deadleg optimized design (low hold-up volume, small wetted area, minimal dead spaces)
High-grade surface finish down to Ra 0.25 µm and EHEDG-certified diaphragm seal system
GEMÜ modular system with high-quality components (actuators, diaphragms, valve bodies, position indicators and positioner or process controllers) that are synchronized with each other
Customer benefits
Simplified documentation and validation (e.g. less radiographic inspection)
Low space requirement
Optimization of production and operating procedures
Expertise and copy protection
Lower installation time, simplified commissioning and servicing
Reduced and/or simplified inventory (e.g. fittings)
Greater flexibility and lower costs during simultaneous implementation of a modular system design
Simplified validation and documentation
Increased product reliability
Increased operational safety
Complex processes using welded assemblies are often still being implemented today, more than 20 years after the market launch of the first M-blocks. The valves, fittings and pipe components used for this require a lot of space, a greater installation and welding effort on site and lead to a correspondingly high validation expense. Not to mention a high hold-up volume and larger deadlegs in compliance with the conventional 6D or 3D rules.
GEMÜ solution for safe operation and high-quality products
Over the years, GEMÜ has implemented over 400 different designs and thousands of customized variants of multi-port valve blocks to make processes safer, increase system availability and reduce the life cycle costs of a system as part of a total cost of ownership (TCO) concept.
Consultation, engineering, manufacturing expertise
We begin supporting our customers as early as the planning phase by providing them with ideas and initial drafts. We then implement the design in the 3D CAD system and adjust it to closely meet the requirements of the particular customer. This jointly developed solution is then processed in our highly efficient machine shop. Several thousand blocks, with weights ranging from 0.1 kg to 500 kg, are processed each year on our multi-axis machining centres.
Product advantages
Customer benefits